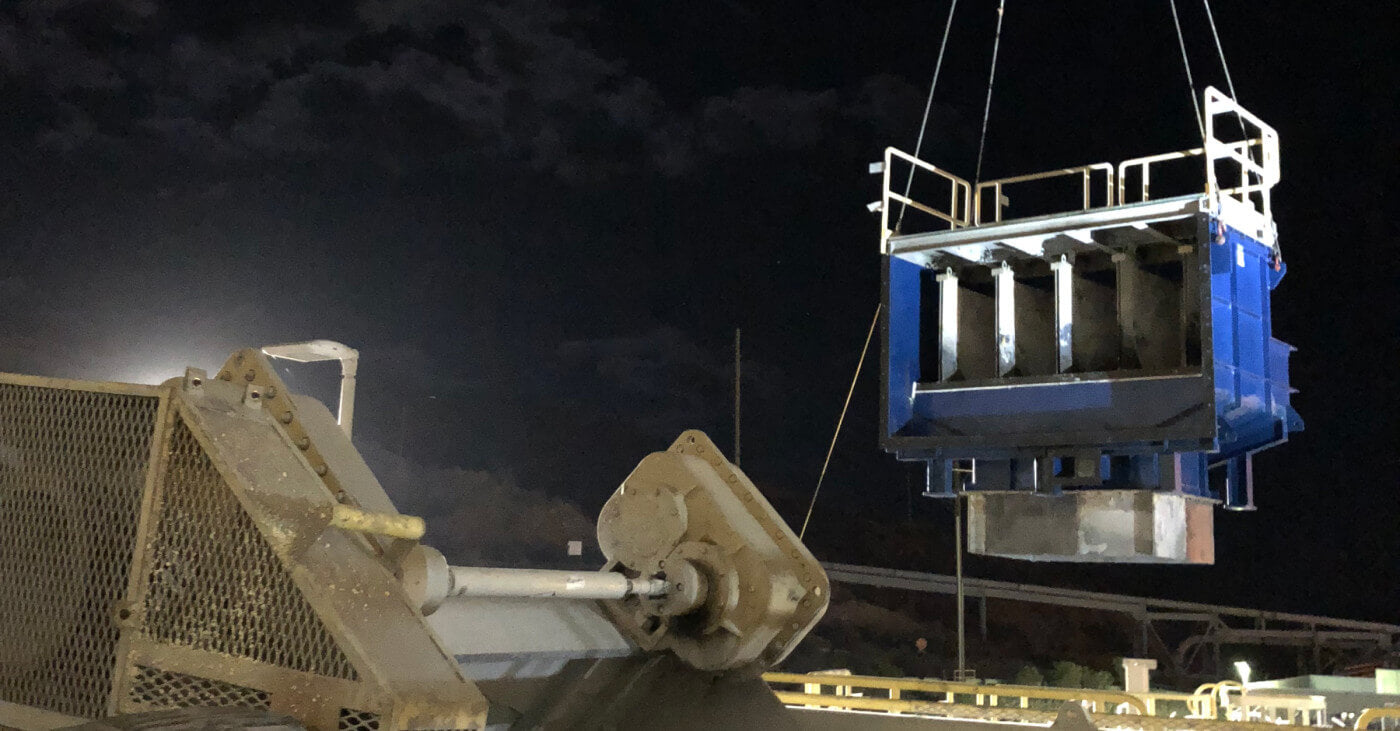
With so much talk of digital manufacturing and Industry 4.0, it’s easy to forget that a lot of fabrication still involves manual processes. Mining is a case in point. Measurements and designs for mining platforms are often done with traditional tools that are inefficient and time-consuming – but 3D scanning offers a smart and accurate alternative.
Titan Engineered Solutions, Inc, an Arizona, US-based company providing custom mining solutions has taken this path. Their client base is the mining industry in the southwestern part of the United States and Mexico. These mines are very large operations with diverse needs and generally located in remote areas. That is where Titan’s expertise comes in.
They specialize in providing responsive engineering services from concept to completion. The products they fabricate are custom and designed to fit precise dimensions. “We do one-off solutions, whether it be lifting devices, wear parts, safety platforms, transfer chutes… You name it – we do it. We’re kind of a one-stop shop for everything mining-related,” Brandon Koch, Titan’s General Manager, says.
Three years ago, Titan’s design team determined that 3D scanning had the potential to automate many of their manual tasks. They made the plunge and bought an Artec Leo, Artec Ray and Geomagic Design X software to help them prepare the scans for SolidWorks.
It made a world of difference in their capabilities. No more tape measures for checking tolerances. No more blind fabrications. Now they scan the entire area where a platform needs to fit and check for interferences before shipping to the client’s site. And an entirely new category of projects was now feasible: reverse engineering obsolete equipment.
Geomagic Design X was a natural choice for Titan because of its compatibility with their native design software, SolidWorks. “I can go straight from solid bodies in Design X to SolidWorks, and that helps a lot for aligning, we can align those bodies in SolidWorks as we’re more familiar with that software. We can align those in SW and bring them back into DX and see the tolerances,” Titan’s designer José Corrales explains.
They use 3D scanning and Geomagic Design X in three ways: identifying collision between platforms and the surrounding area, reverse engineering obsolete pieces and checking tolerances of fabricated parts.
3D scanning for interference avoidance in mines
Safety platforms are a common type of solution that the mines order from Titan. In the past, they would fabricate, without an overview of the area that surrounds the platforms. With each mine shaped differently, every platform must be custom-made. Designing platforms in this way often resulted in interferences, or parts of the platform that collide with the surroundings.
However, 3D scans allow Titan to check for these interferences before the platform is shipped and installed. They scan the area where the platform is going to be installed, design the platform in SolidWorks, open the model in Geomagic Design X and place it inside the 3D scan of the surroundings.
“This will show us the conflicts between the area and the platform we designed. If we were to use a tape measure instead, we might check one thing but miss another. Scanning has helped us in this aspect a lot,” Koch explains.
Checking tolerances of mining solutions with Design X
Another task where Design X has proven to be a time-saver is verifying the tolerances of a fabricated part. Usually, they fabricate a part with a CNC machine and then check the dimensions with a tape measure. Today, Corrales simply scans the fabricated part and overlays the scan with the CAD in Design X for verification.
“In the image you can see how we use the scanners and the scanning software to ensure the fabrications are within tolerance.” Koch says. “It’s crucial to do this before we ship them to the site since most products are large and heavy and shipping is costly and time-consuming.”
Heat mapping is another advantage that comes with using Design X. “It allows us to set tolerance to plus or minus 1/16 inch and see how far out we are, and if it’s a critical area or non-critical. Heat mapping is a much more efficient way of ensuring that we’re within tolerances than using a tape measure,” Koch explains.
“Our clients also really like the heat mapping. They can see from blue to red how far off we are in some areas and how close we are in others and if you’re hitting those critical points.”
Reverse engineering for mining
Finally, scanning allows Titan to do more reverse engineering of obsolete equipment. Mines often need reverse engineering services as a lot of things are manufactured in the field. A contractor goes on the site and fabricates the piece there and then, when it wears out, mines need a fast way to remanufacture them.
Rather than pulling a tape measure and doing a napkin sketch, Koch and Corrales scan a part, take the scan data from the scanner to Design X and convert the mesh into a solid body. They finalize the model in SolidWorks.
“We use the scanners religiously for complex stuff, like a transition that goes from square to round, an oval or an odd shape. We’re able to use them through the design process and verification to ensure that what we’re supplying is what they require,” Koch says.
Heat map of existing vs modeled piping system
Measurement made easy with 3D scanning
A common thread in all these uses is that measuring has become faster and more accurate. When they were measuring with tape, Titan often had to send two employees to a site. Nowadays, it’s just a sales representative and a scanner. Less effort, less time, and more data.
Additionally, scanning eliminated the possibility of human error. “When you measure manually, people make mistakes and sometimes transcribe the numbers incorrectly. Then you produce the item, ship it on-site and it doesn’t fit. But 3D scanning doesn’t lie and there’s no room for human error – it's one of the most trustworthy employees we have.”
Edited:
Rapid Scan 3D wasn't just about selling 3D scanners; we offered a complete solution that would fit their needs. To streamline their workflow Rapid Scan 3D combined the Artec Ray and Artec Leo with Artec Studio software improve efficiency. "One of the amazing features that Artec 3D provides is the integration of all 3D scanners within one software. You can utilize the Artec Ray with Artec Leo in the same project and combine the data from long and short range data. This allows companies like Titan to have the best in industry technology and mobility of Artec 3D scanners" said 3D scanning specialist Chris Strong.
Rapid Scan is an authorized Artec 3D and Geomagic Reseller
www.rapidscan3d.com
info@rapidscan3d.com
(562) 912-3544
Original Article: https://oqton.com/posts/titan-use-geomagic-designx-for-mining-solutions/