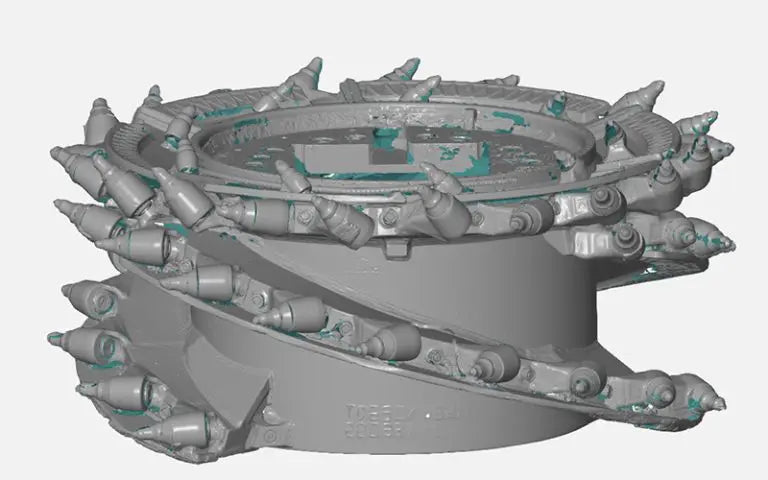
Underground mine sites require heavy-duty equipment to explore and develop the mineral resources. The equipment has various functions, such as breaking and extracting the rocks, processing the ores, and restoring the land after the mine is closed.
Underground mining has different challenges than surface mining, and it needs specially designed mining machinery to cope with them. It is important to keep the equipment in good condition and ensure its optimal performance.
Huangling Mining Group CO, Ltd, a subsidiary of Shaanxi Coal and Chemical Industries Group, operates multiple mines and is a prominent player in the energy sector.
Facing challenges in the repair process for cutters of mining machines, the company sought an innovative solution that would streamline the repair process and improve efficiency. One such solution is “3D scanning”.
Customer Challenge
The milling drum of the mining machine has various cutters attached to its surface. The cutters, made of hard materials to withstand the abrasive conditions encountered during mining, are inserted into bushings which are welded to the surface. The shape and arrangement of the cutters are crucial for the efficient extraction of coal.
Wear and Damage: Continuous use of the cutters under demanding mining conditions can lead to wear and damage. The cutters may become dull, fractured, or even completely worn down, affecting the drilling efficiency and coal extraction.
Costs: Repairing cutters and bushings can be costly, especially if significant damage has occurred or if multiple cutters need replacement. The cost of materials, labor, and downtime of the mining machine can all contribute to the overall expense.
Conventional Method
Traditionally, repairing these cutters involved removing and replacing each small cutter individually, creating a labour-intensive and time-consuming process.
Additionally, the bushings for the cutter needed to be welded to the milling drum, resulting in further inefficiencies and costs. The customer sought a more efficient and effective method to repair the worn-out cutters.
Solution: KSCAN-Magic Composite 3D Scanner
To address the customer’s challenges, Scantech offers composite 3D scanner KSCAN-Magic to capture the complex geometry of cutters. The worn-out parts were subjected to 3D scanning, enabling a visual analysis of the wear of cutters and bushings.
KSCAN-Magic is an advanced composite 3D scanner that uses both infrared and blue lasers to suit various needs.
This versatile device offers five modes of operation including blue laser crosses for ultra-fast scanning and blue parallel lasers for hyperfine scanning. KSCAN-Magic performed well in capturing the fine details of these cutters with high accuracy.
The KSCAN-Magic 3D scanning were combined with laser cladding to repair the cutters. Laser cladding is a technique for adding one material to the surface of another using a laser beam as the heat source.
The material is melted and fused to the surface, creating a coating. Laser cladding can be used to repair damaged or worn parts, protect them from corrosion or wear, or create complex shapes from scratch.
Based on the data obtained from the scanning, the engineer used laser cladding to refurbish the worn part to its original state.
As parts get worn, they are renewed by 3D scanning and cladding, instead of scraping the entire part. This solution eliminated the need for removing and replacing each small cutter. And there is no need to remove bushings and weld new ones, resulting in a streamlined repair process.
Advantages of Scantech’s 3D Solutions
High Precision and Efficiency
KSCAN-Magic has an accuracy of up to 0.020 mm, which ensures engineers conduct accurate measurements. KSCAN can measure surfaces efficiently, thanks to its high measurement rate of up to 4.15 million measurements per second. This saves a lot of time and money and improves inspection quality.
Efficient and Cost-Effective Repair Process
The implementation of 3D scanning and laser cladding eliminated the traditional labor-intensive and rough repair process. This led to significant time and cost savings for the customer.
Furthermore, the reduction in consumable items, such as the need to prepare bushing for holding small cutters, resulted in additional cost efficiency.
Enhanced Maintenance Capabilities
By incorporating scanning and laser cladding technology, we showcased a new approach to maintenance procedures in the mining industry.
This innovative technique provided the customer with enhanced capabilities for refurbishing and reusing worn cutters, eliminating the need for frequent replacements and reducing operational downtime.
Conclusion
Through the adoption of 3D scanning and laser cladding technology, Scantech helped Huangling Mining Group successfully transform the repair process for mining cutters.
The implementation of this innovative solution not only improved the efficiency and effectiveness of the repair process but also showcased the ability to embrace new techniques in an industry often constrained by traditional methods.
By providing the customer with a new idea, the scanning and laser cladding technology enabled Huangling Mining Group to enhance its maintenance capabilities and open avenues for further adoption of this approach across the mining and maintenance industries.
For more information on the Scantech 3D scanners for the Oil and Mining Industry please feel free to contact one of our 3D scanning specialist.
Rapid Scan 3D
E: info@rapidscan3d.com
P: (562) 912-3544 e
W: www.rapidcan3d.com